Slow Conveyor System AIRCONDOS with Bypass
The Aircondos system is a pneum. dense phase conveying system for the energy saving and gentle transport of powdery, granular, heavy-body, sticky or abrasive products. The main difference to the known dense phase conveying systems (shear conveyors) is that conveying and fluidizing air is fed into the conveying line via a bypass line along the entire conveying section: Picture 2011
The air or gas (e.g. N2) is fed in via gas metering devices which are arranged at certain intervals on the delivery line depending on the product to be conveyed. The conveying speed can be kept almost constant by expanding the pipeline cross-sections. A supercritical pressure ratio in the gas dosing device generates sound velocity. This technical solution ensures that a defined amount of air constantly flows through each blow-in point. This means that material plugs forming in the pipeline are always dissolved by the Aircondos system so that flawless dense flow conveying is ensured.
If this bypass conveyor would be equipped without the Aircondos system, there is a risk of clogging the conveyor line because the injection air chooses the path of least resistance, i.e. the air escapes through the free injection points.
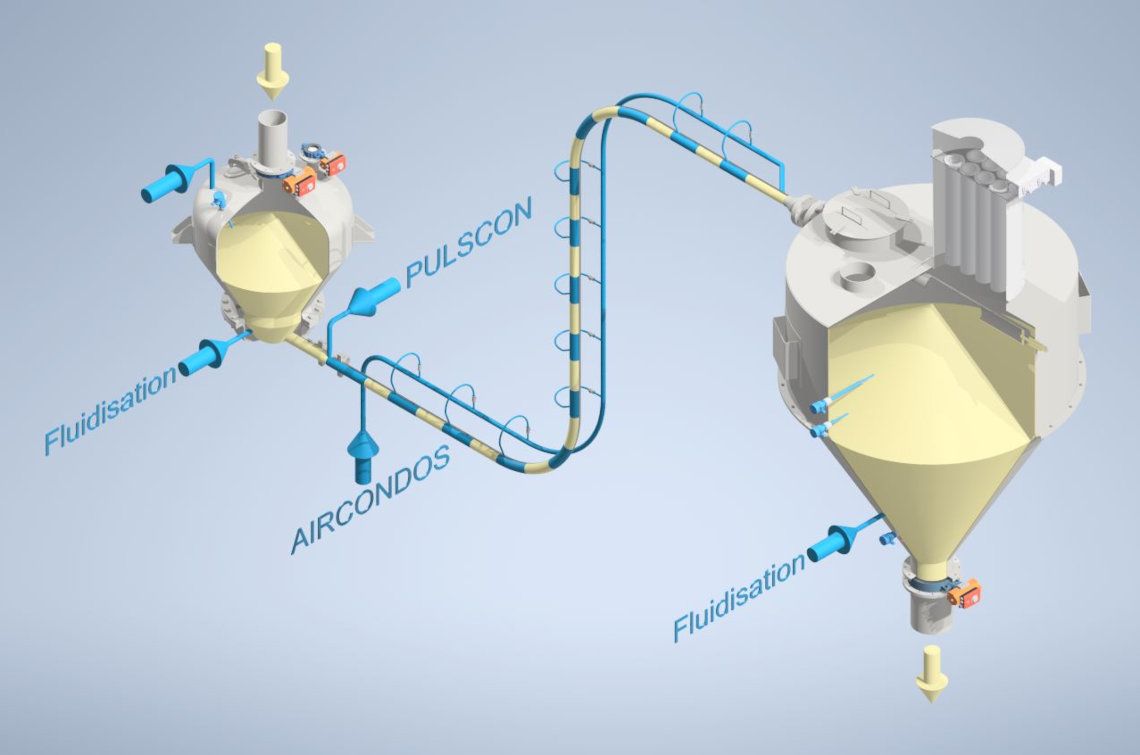
The advantages of this system are:
- The conveying speed can be reduced to low values:
From approx. 0.5 m/s to normally 5 to 8 m/s - The line does not have to be emptied
- With most products, the line can be restarted filled.
- This is particularly advantageous after an emergency stop, as the pipeline does not have to be mechanically cleaned and emptied before it can be conveyed again.
- Products with poor flow can be conveyed safely.
- Sensitive products such as marble sands can be conveyed slowly and gently.
- By conveying the product in the dense phase process, a segregation of the product into coarse and fine particles is counteracted.
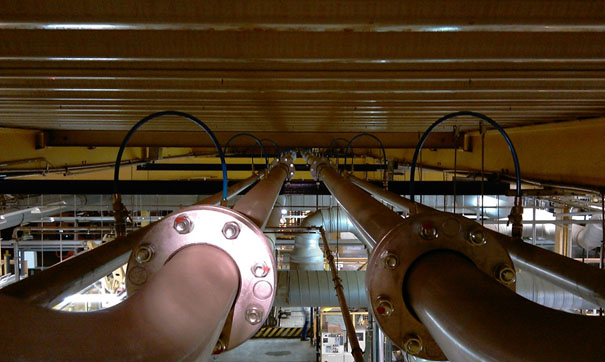
Some selected examples of executed Aircondos systems:
- TiO2 for the paint and lacquer industry Corundum conveying for the abrasives industry: Extremely abrasive product (Mohs hardness 9.3, in comparison: diamond hardness 10.0). Conveying distance 90 m into different receiving containers Requirements: the sharp-edged crystalline shape of the individual corundum grain must not change during conveying. Additional metal inclusions due to wear of the steel conveying lines must be reduced to a minimum. When changing products, e.g. from red to white, product mixes must be excluded. The service life of the system must be at least twice that of mechanical systems. Maintenance and cleaning times must be negligibly short. The task was solved with the Aircondos system, in which conveying speeds (0.2 to 0.8m/s and air volumes are extremely low. By means of an additional device, the entire system can be cleaned down to the last grain within 30 seconds.
- Lead dust (mill dust, cardboard dust, lead powder, etc.) for battery production: Lead dust, especially mill dust, tends to adhere and clog up in the pipeline. Points with a long service life must be used to mix different dusts. Start-up dust must be stored separately and added in doses. The discharge from the silos must be trouble-free and unproblematic. It must also be possible to start up the pipeline again in full condition. The fluidized transmitters and the Aircondos conveying system with Pulscon enable trouble-free transport of lead dust. Even the transport of mill dust directly after the mill filter (without day silo) is possible without any problems. The lead dust from different mills or reactors can be mixed in one silo or distributed to different silos through the pipes with specially developed points. Start-up dust is stored in a freely selectable silo and metered added to the normal dust. The silos are discharges via fluidiser discharges in the silo cone. They ensure a trouble-free discharge of the stored material and bridge formation as well as material accumulations in the transition from the cylindrical silo part to the silo cone are minimised.
- TiO2 for the paint and lacquer industry: TiO2 is defined by TiO2 manufacturers as non-pneumatic conveyable. The very adhesive powder is extremely difficult to convey. Pipelines are growing and tampers are high on the agenda with conventional conveyances. Discharging from the silo is considered extremely difficult, as the product compacts and adheres to the silo wall. With our fluidized transmitters together with the conveying system Aircondos and the Pulscon plug conveying it becomes possible to convey TIO2 trouble-free also over longer distances. Discharge from the silos is realised by means of fluidiser discharge aids in the silo cone (see chapter Silo systems: Fluidisation discharge aids).
- Perlite conveying for the insulation and filter industry: The bulk density and the grain structure, e.g. 0.06 kg/l, may only change by a maximum of ± 4.5%. Tests with conventional pneumatic conveying systems have shown adverse volume changes of up to 46%. Below are the results of extraction with Aircondos.
- Silicon for the photovoltaic industry: Silicon with Mohs hardness 7 should be conveyed over long conveying distances (150 distance at 50 mheight difference as wear-free as possible. long service life of the pipeline must be guaranteed. Segregation of the product must be prevented. High ambient air temperatures of over 50 °C. The material to be conveyed must not come into contact with oxygen. The material is conveyed by means of N2 as inert gas. For reasons of wear, the complete delivery line is designed as a fused basalt pipe. The Aircondos bypass system is used as the conveying system. This also effectively prevents segregation of the product during conveying. Additional measures during feeding and discharging into and out of the silo through various silo filling pipes also prevent segregation there. This allows the material to be conveyed very slowly and with little wear. The pipeline and the bends achieve a very long service life. The N2 or oxygen content is monitored and controlled
- Sands and cements for the building materials industry: The grain size may not or onlyinsignificantly change due to pneumatic transport. The proportion of fines (powder) must not increase significantly. Gentle slow conveying with conveying speeds from 0.5 m/s ensures gentle transport of the product.
- Conveying of metal powder mixtures: Segregation during conveying is not permitted. The ingredients contained in the mixtures such as metal powder, copper, coal dust, sulphur, nickel, lubricants etc. have different bulk weights of 0.3 to 4.0 kg/l and grain spectra. Some substances are also added in very small quantities, so that even the slightest segregation of the material to be screened has major consequences.
After pressing and subsequent sintering, the mixtures conveyed with the Aircondos produce high-quality, uniform products.